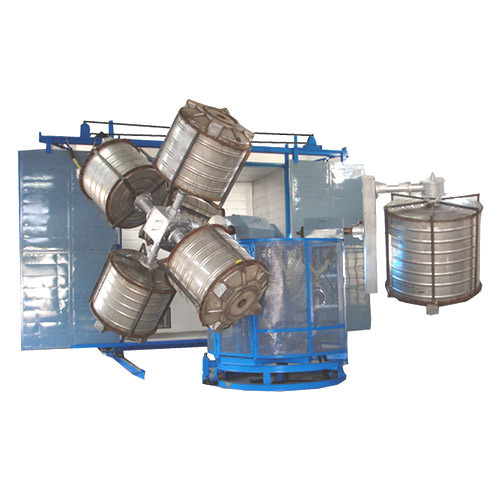
Rotational Molding 101: Understanding the Basics of the Process
Rotational molding, a manufacturing strategy widely used for developing hollow plastic-type merchandise, requires a fragile harmony of art and science to achieve ideal results. Here’s a deeper plunge in to the intricacies of mastering this innovative procedure:
Optimizing Material Assortment:
Picking the right material is very important for effective rotational molding. Factors such as UV opposition, chemical substance compatibility, and mechanised components needs to be regarded based on the product’s planned app. Polyethylene remains to be the most commonly employed material because of its overall flexibility, durability, and cost-performance.
Mastering Mildew Design and style:
Mildew design plays a crucial part in rotational molding. Accomplishing standard walls size, suitable write facets, and sophisticated features demands careful consideration in the layout cycle. Advanced CAD application and simulation tools support technicians optimize mildew geometry for optimum efficiency and component quality.
Good-Tuning Approach Variables:
Dealing with approach variables like home heating temperatures, rotational speed, and air conditioning time is essential for making higher-high quality elements. Exact temperatures management guarantees constant materials stream and syndication, when best rotational speed prevents substance pooling and uneven wall surface density.
Implementing Good quality Guarantee Measures:
Top quality confidence is crucial on the rotational molding approach. Assessment methods such as ultrasonic testing, aesthetic assessment, and pressure testing assist determine flaws at the beginning of the development routine, making sure only pieces conference stringent high quality standards are sent to clients.
Adopting Innovation:
Continuous innovation drives developments in rotational molding technologies. From automation and robotics to sustainable materials and additive production techniques, embracing technologies boosts approach effectiveness, minimizes steer instances, and expands the options for product or service customization.
Collaborating Across Disciplines:
Effective rotational molding requires collaboration across multiple disciplines, which include design and style, technology, resources scientific research, and production. By fostering interdisciplinary teamwork and data expressing, producers can leverage combined expertise to beat obstacles and travel advancement.
Making an investment in Coaching and Education:
Education and schooling are necessary for building experienced pros competent at mastering the art of rotational molding. Fingers-on instruction courses, workshops, and sector certifications encourage people with the data and expertise required to master this specialized field.
Verdict:
Perfecting the art of Rotational Molding demands a holistic technique that includes material variety, mildew design and style, procedure search engine optimization, quality certainty, creativity, collaboration, and ongoing instruction. By embracing these principles and continuously refining their strategies, companies can open the full probable of rotational molding and supply exceptional goods that fulfill the changing requires of customers and sectors.
Proudly powered by WordPress. Theme by Infigo Software.